5 Warehousing Factors to Look From A Fulfillment Center
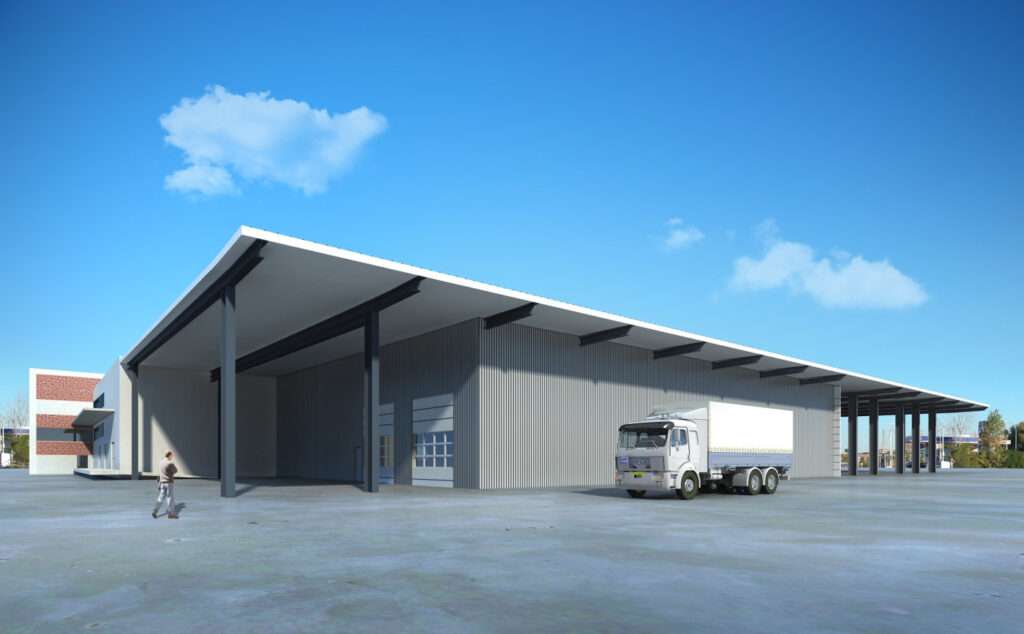
Most e-commerce entrepreneurs ignore warehousing systems probably because many of them aren’t connected enough with their warehouses. After all, that’s one of the reasons they hire fulfillment centers – so these centers will do the warehousing work for them. Of course, we will do your warehousing work for you, but it’s good you know what […]