Understanding Reverse Logistics: An Ultimate Guide for Effective Operations
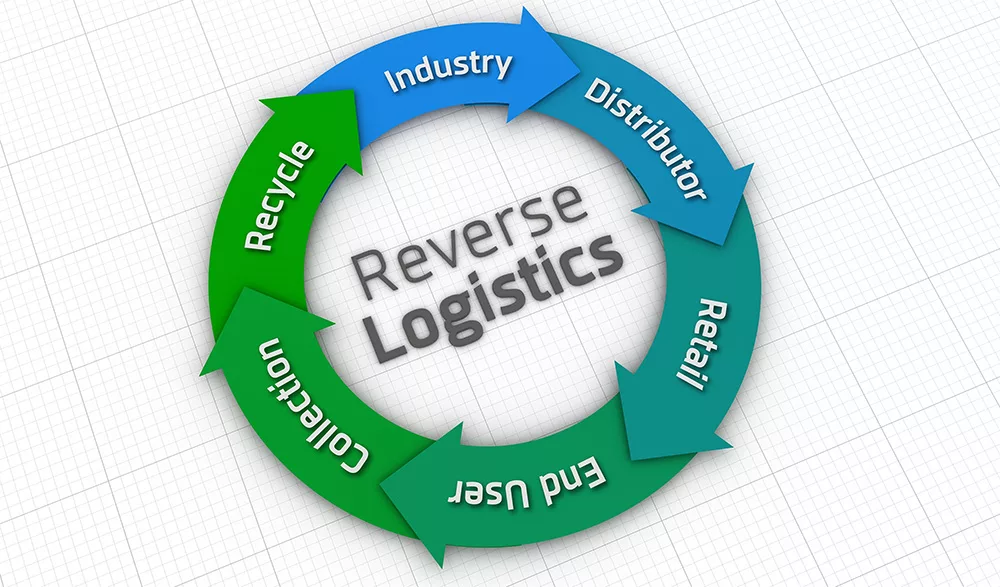
In today’s competitive business landscape, efficient management of the supply chain is crucial for the success of any company. While traditional logistics focuses on the forward movement of goods from manufacturers to end consumers, reverse logistics plays an equally important role in handling product returns, repairs, recycling, and more. In this blog post, we will […]
How Do You Pick the Right Shipping Carrier? An Ultimate Guide
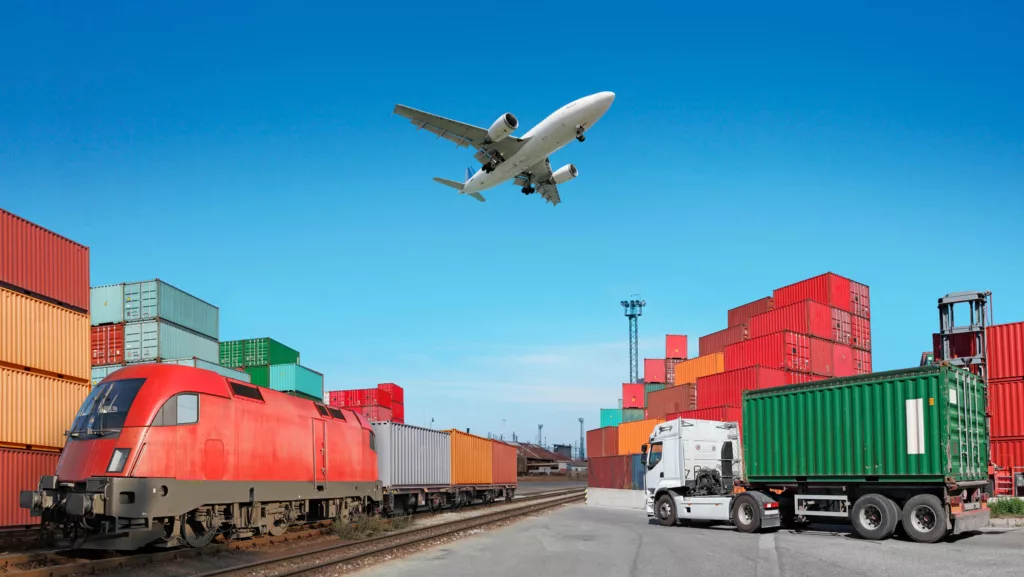
When it comes to running an e-commerce business or even shipping personal packages, choosing the right shipping carrier is crucial. With numerous options available, selecting the most suitable carrier can have a significant impact on your overall customer experience and business success. In this article, we will discuss what a shipping carrier is and provide […]
Streamline Your E-commerce Operations: A Quick Guide to WooCommerce Fulfillment
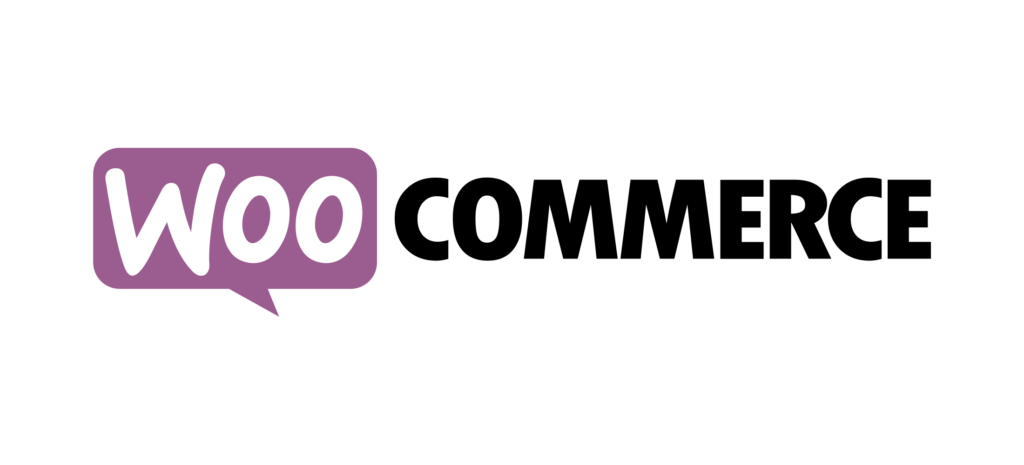
In the rapidly evolving world of e-commerce, efficient order fulfillment is key to maintaining customer satisfaction and driving business growth. For WooCommerce store owners, optimizing the fulfillment process is crucial. This quick guide will provide you with valuable insights into WooCommerce fulfillment, including practical tips and techniques to streamline your operations. Moreover, we’ll explore the […]
An Ultimate Guide to Shopify Fulfillment: Streamline Your E-commerce Operations
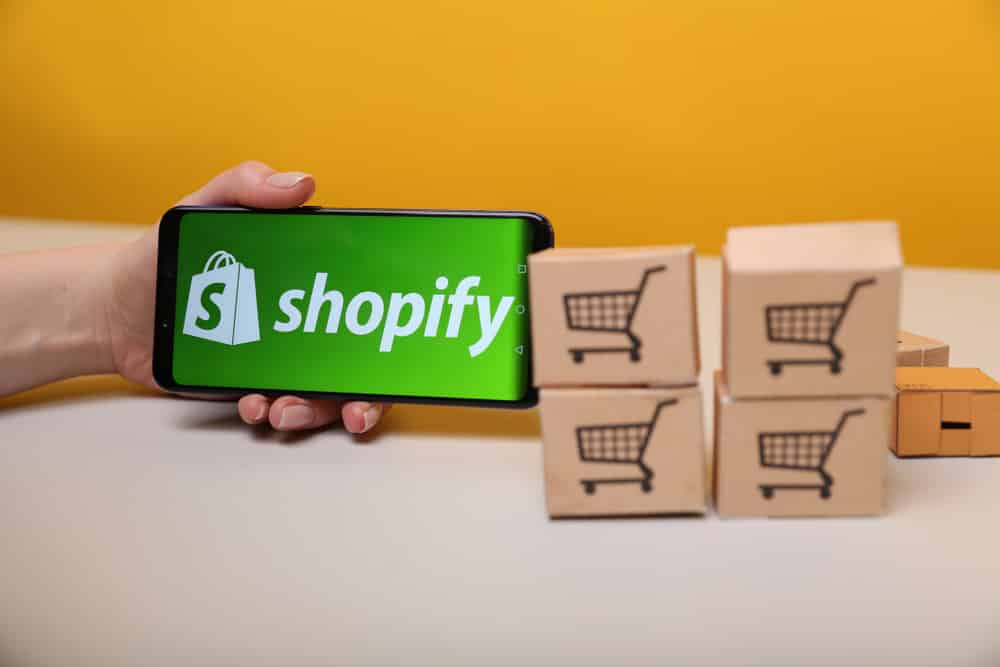
Shopify, one of the leading e-commerce platforms, offers a robust order fulfillment system that empowers businesses to deliver products seamlessly. In this blog post, we will explore the concept of Shopify fulfillment, its importance, how it works, different service options available, and factors to consider when choosing its service. What is Shopify Fulfillment? Shopify order […]
Dropshipping vs. Amazon FBA: An Ultimate Comparison in 2023
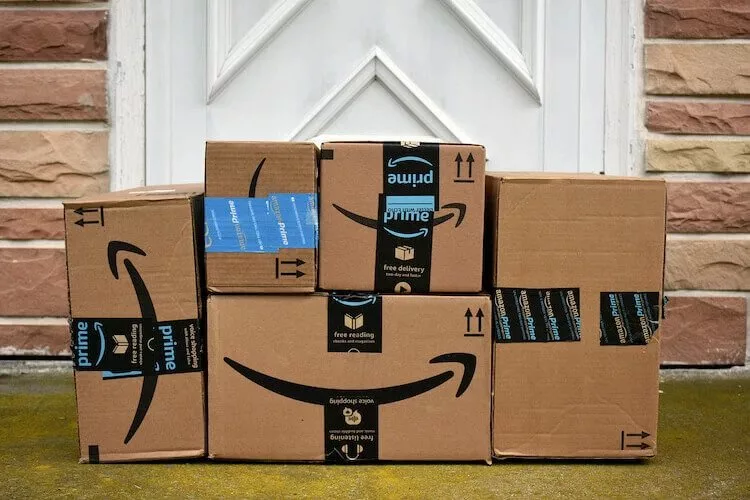
In the ever-evolving world of e-commerce, two popular business models have gained significant traction: Dropshipping and Amazon FBA (Fulfillment by Amazon). Both approaches offer unique advantages and challenges, making it crucial for entrepreneurs to understand their differences and choose the right path for their online business. In this blog post, we will delve into the […]
Understanding the Role of a Logistics Service Provider: An Ultimate Guide
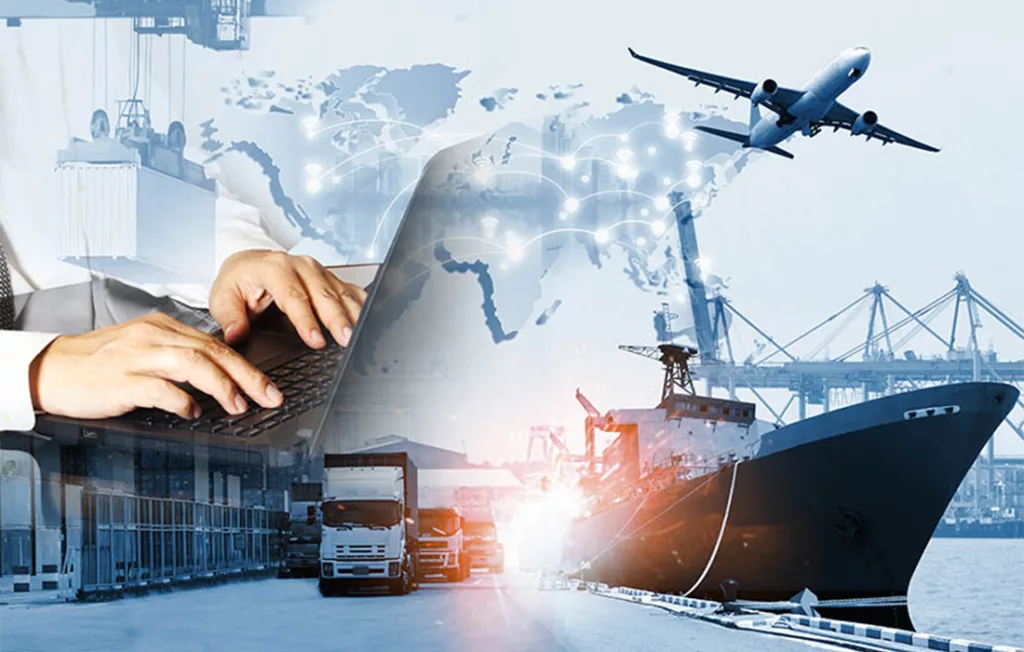
Iffective logistics management plays a crucial role in ensuring the smooth flow of goods and services in today’s fast-paced and interconnected business world. As companies strive to optimize their supply chain operations, partnering with a reliable logistics service provider has become increasingly popular. In this article, we will delve into the concept of a logistics […]
Streamline Fulfillment and Cut Costs with Shipping API Integration: An Ultimate Guide
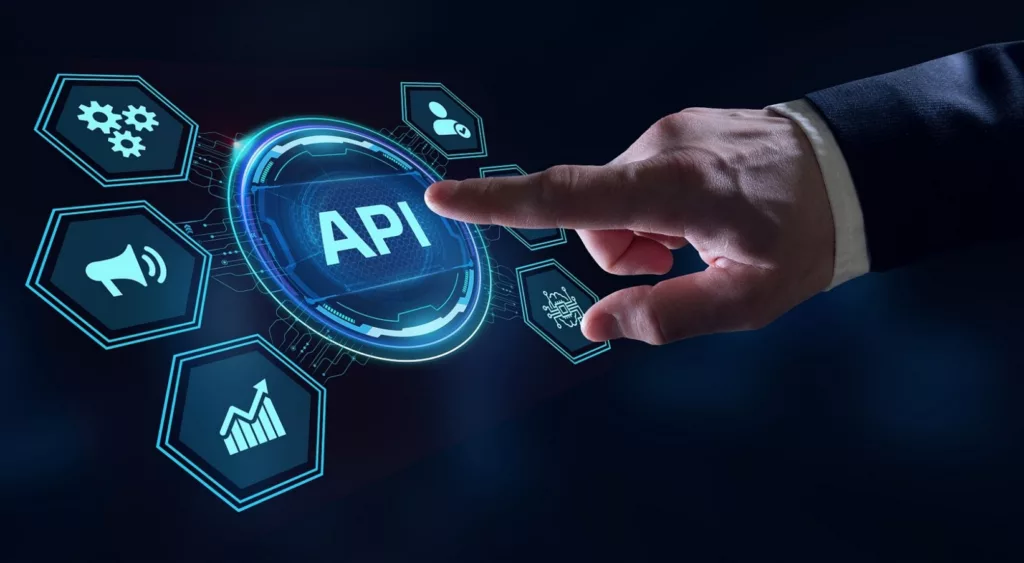
In the fast-paced world of e-commerce, businesses are constantly searching for ways to enhance fulfillment processes and reduce costs. One powerful solution that has gained significant popularity is integrating a shipping API (Application Programming Interface). By automating fulfillment tasks, businesses can achieve greater efficiency while saving money. In this blog post, we will explore how […]
Maximize Profit Margins and Customer Insights with D2C Fulfillment Solutions
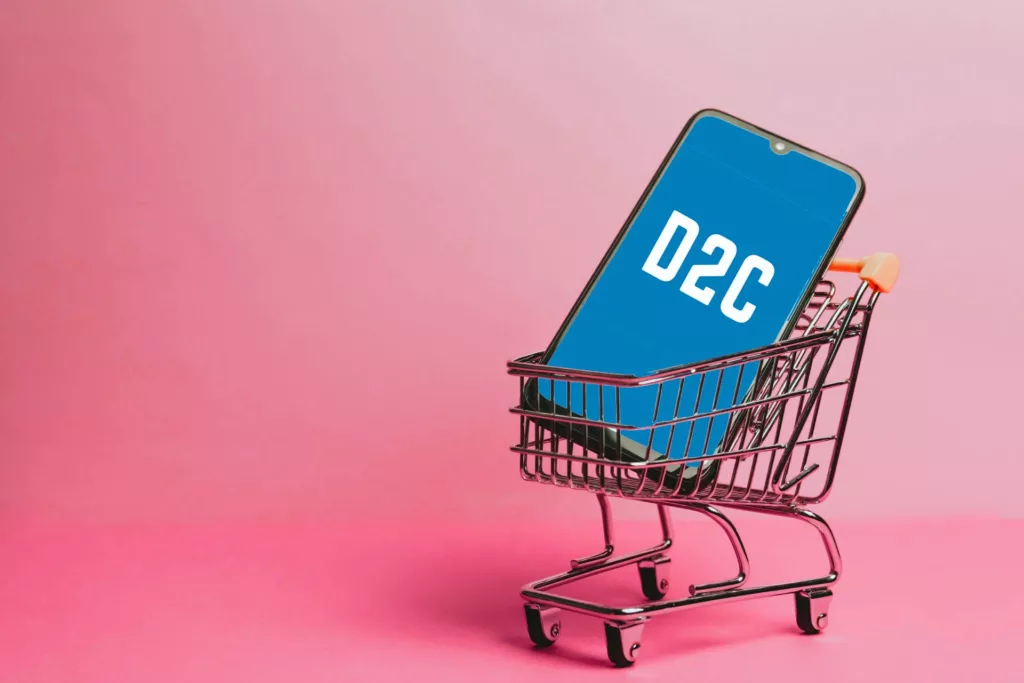
In today’s rapidly evolving business landscape, companies are continually seeking new ways to connect with customers and streamline their operations. One approach that has gained significant momentum is the Direct-to-Consumer (D2C) strategy. This article will delve into the world of D2C fulfillment e-commerce. The article will discuss its specifics, marketing strategies, key differentiators from traditional […]
Hong Kong Shipping to USA eCommerce Guide: Your Ultimate Resource for Affordable Shipping Solutions
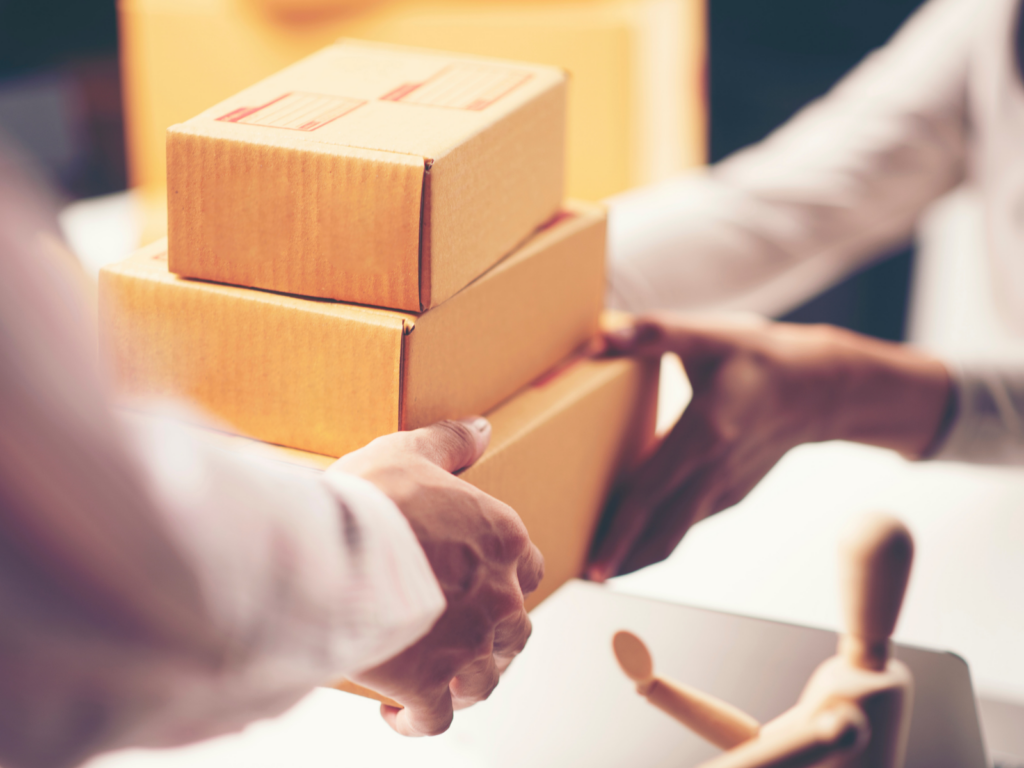
Hong Kong has established itself as a prominent hub for eCommerce, offering a wide range of products to consumers worldwide. If you’re an eCommerce entrepreneur based in Hong Kong looking to sell your products in the United States, it’s crucial to understand the ins and outs of shipping. In this comprehensive guide, we will explore […]
From Cost Savings to Quality Control: Why China Sourcing Agents is Vital for Online Sellers
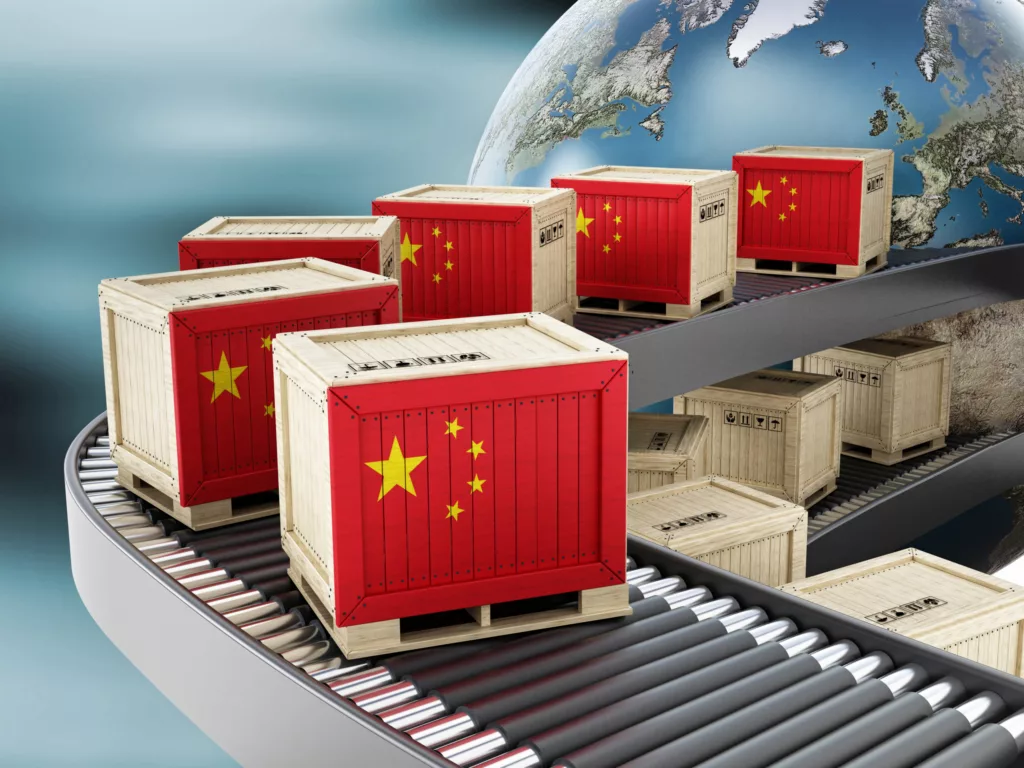
In today’s global marketplace, online sellers are constantly seeking ways to maximize profits while maintaining the quality of their products. Sourcing from China has become an increasingly popular strategy due to its competitive manufacturing costs and vast supplier base. However, navigating the complexities of international trade can be daunting, which is why enlisting the expertise […]